Miniaturization of products
Considering the size is wise. When calculating our products' carbon footprint, it became more evident than ever that the slimness of our products matters. In recent years, technical barriers in fiber optic technology have been overcome, presenting the possibility of using slimmer fibers in our cables. Fibers with a diameter of 250 microns can be replaced with fibers of 200 microns or even 190. Slimmer fibers give slimmer cables and, in turn, the option of slimmer ducts.
The carbon footprint of slimmer fibers and cables is less. However, the major reduction for the solution comes from choosing a slimmer duct. When producing a slimmer duct, we need less material production, and with smaller sizes, transportation decreases. That the products are easier to handle and install is, of course, a welcome bonus. You can read more about why it is wise to choose slimmer products in this article.
Recycled material
Our comparison study clearly showed that products made from recycled or reused material have a lower carbon footprint. The virgin material used in our products accounts for a significant part of our total emissions, and replacing it with recycled material will reduce the carbon footprint. The material we use for our recycled ducts is selected to provide the same quality and life length as the virgin material. Therefore our sources of recycled materials come from:
- Post-industrial material - for example, products brought back from the field by our installers and leftover material from production.
- Post-consumer material - selected high-grade and quality-controlled post-consumer material from a single source.
Why green ducts are black
By using every single piece of leftover duct in production, whatever the color, we can give the material a new life as recycled ducts. The result of this mix of colors is a greener duct in black with a significantly lower carbon footprint than ducts made of virgin material.
Other sustainable materials
Another way to go is to replace oil-based polymers with bio-based plastic. Bio-based plastics are made from crops, a renewable resource, whereas oil-based plastics are made from non-renewable fossil fuels. The production of bio-based plastics also results in lower greenhouse gas emissions compared to oil-based plastics. This is because bio-based plastics use less energy during production, and the feedstocks absorb carbon dioxide during growth.
Renewable energy in production
Transitioning to renewable energy is vital for reducing the environmental impact of our production facilities. We proudly announce that all three European production sites in Sweden, Austria, and the Netherlands, run on renewable electricity. The majority is hydropower and wind energy, but the mix also includes solar and bioenergy.
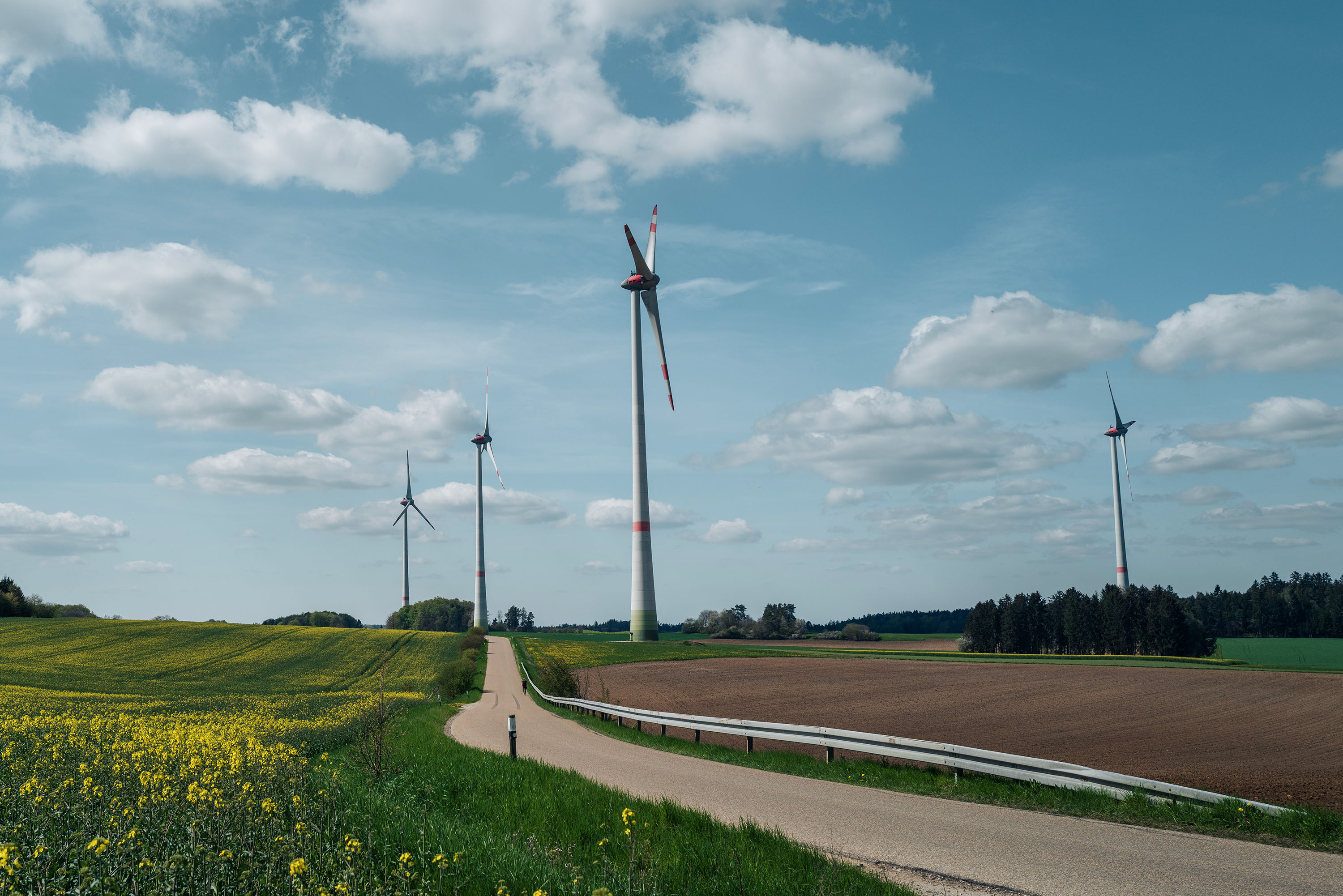